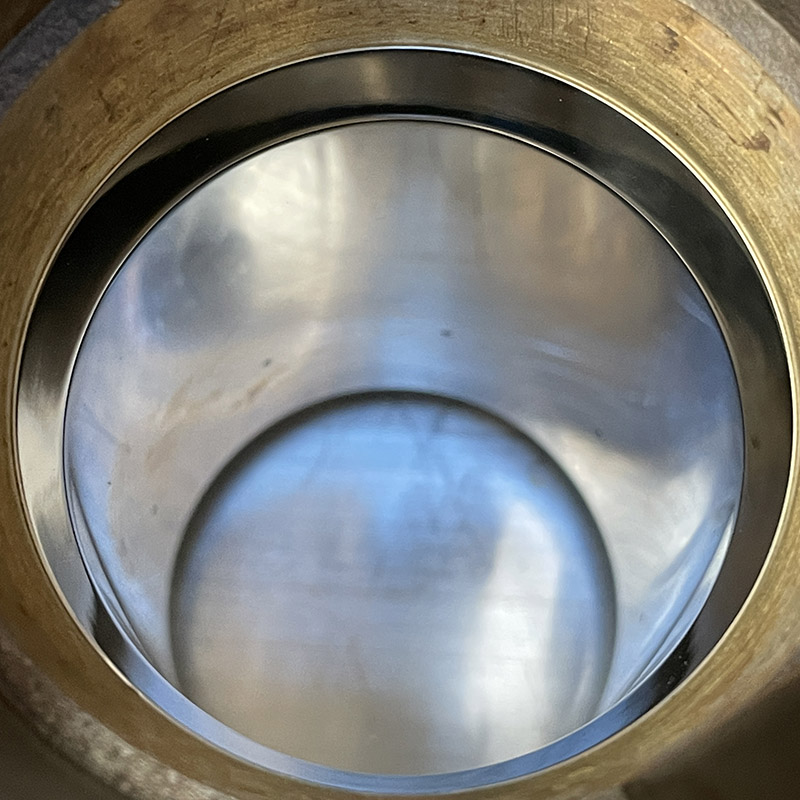
What is new for the 3rd edition?
The group is getting a few modifications. The original design comprised two castings: the main body and a short sleeve, that were thermally shrink-fit together and machined after assembly.
We have replaced the second casting with an AISI 316 sleeve that lines the entire bore of the body. As well as being easier to manufacture and thermally indistinguishable from the all-bronze version, the sleeve has benefits for water distribution. First, it is compatible with E61 slip-on shower screens; we now use a 35µm mesh screen which we found gives the best results after considerable testing. Second, a radial channel around the outside of the sleeve distributes incoming brew water and injects it into the brew chamber via 8 ports instead of the single port in the original design.
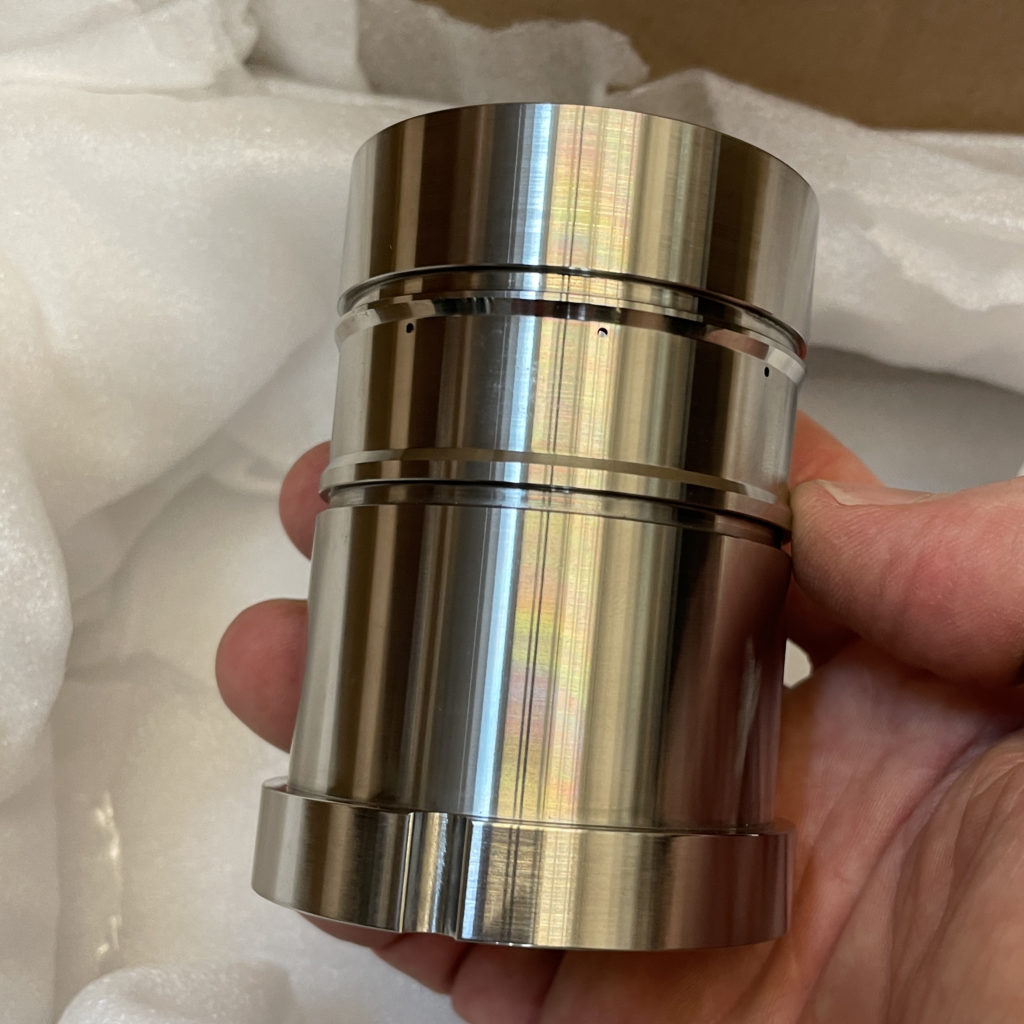
These two changes improve the symmetry of the water flow into the chamber and result in a reduction in turbulence above the puck. We have also moved away from bronze to stainless for the cam for strength and longevity and to reduce our use of chrome – which we do wherever possible for environmental reasons.
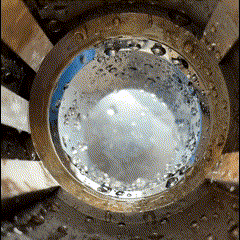
The other changes, with a few exceptions, are incremental improvements that either simplify or improve the stuff under the hood. This is done not just to streamline the manufacturing and assembly process, but to build a more robust machine – in short: the simpler it is, the less there is to go wrong. Changes like this include a redesigned boiler that makes welding (slightly) easier, a new, stiffer, laser-cut 3D jigsaw puzzle frame, a reworked hydraulic system to reduce component count and to make assembly and maintenance easier, some streamlining of the wiring harness and the elimination of a couple of internal plastic parts.
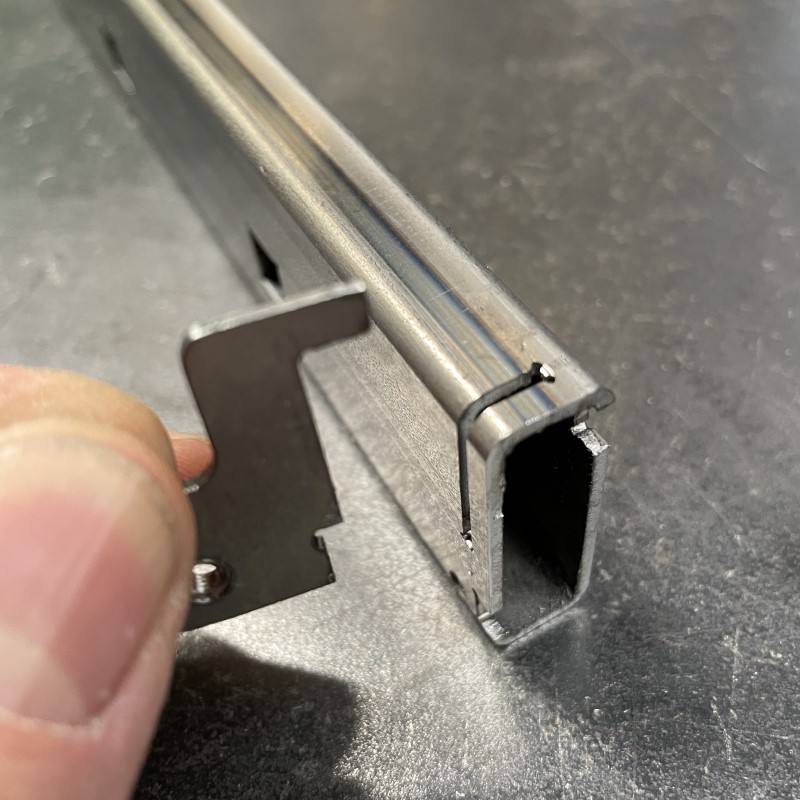
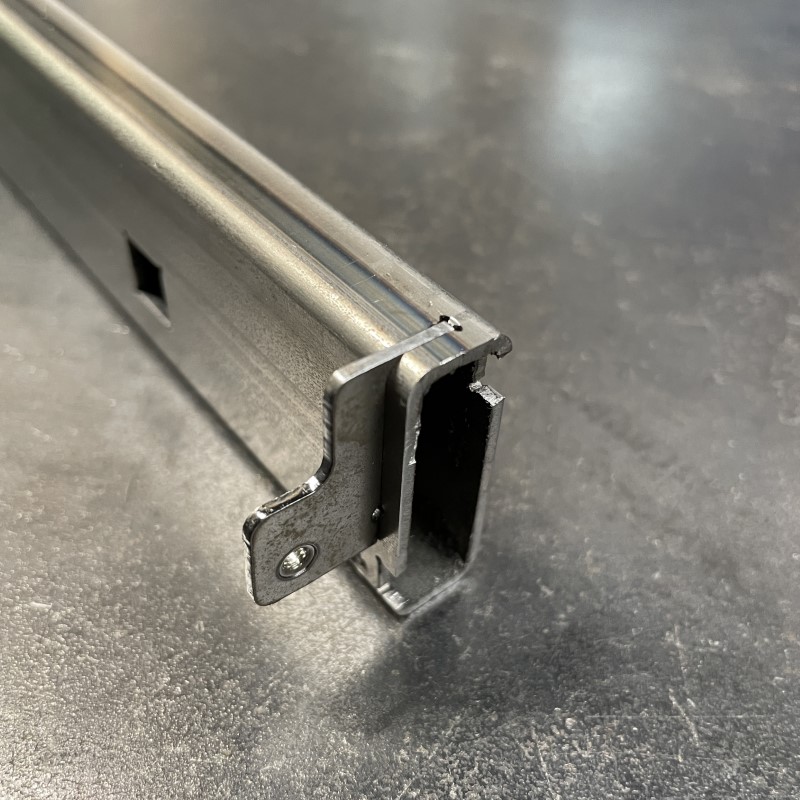
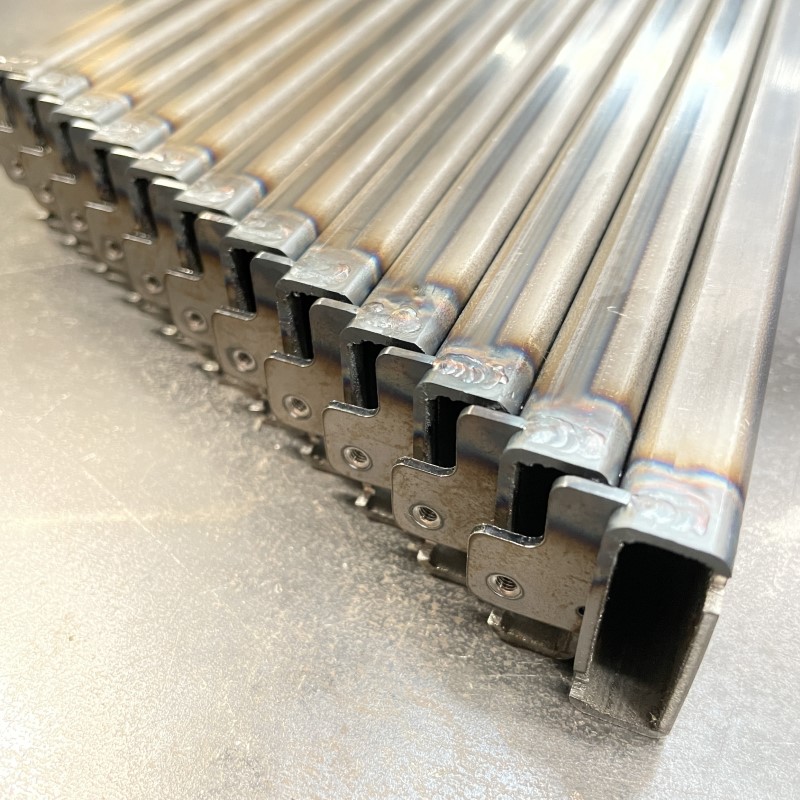
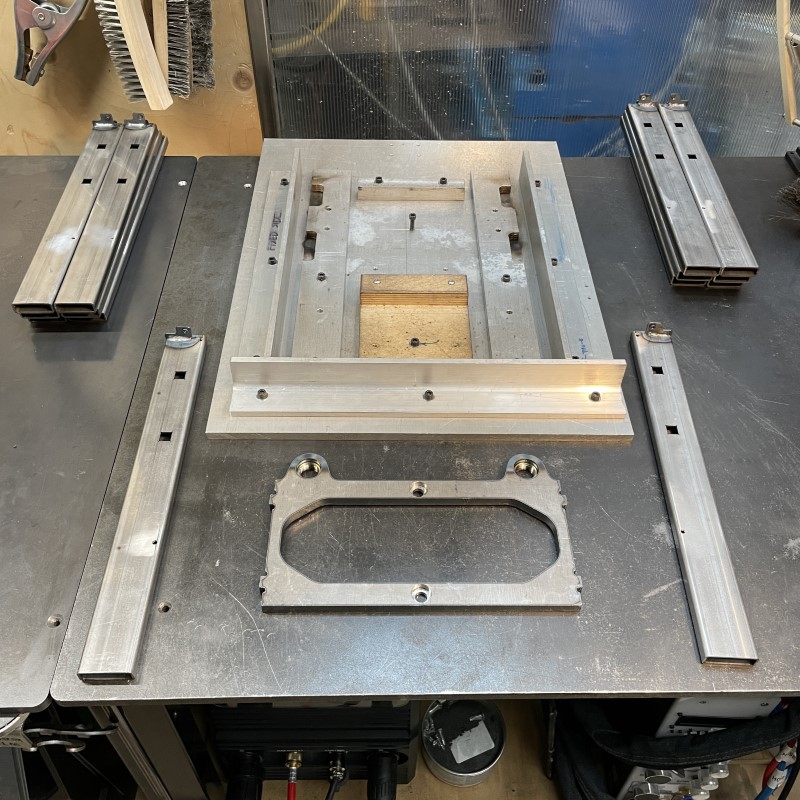
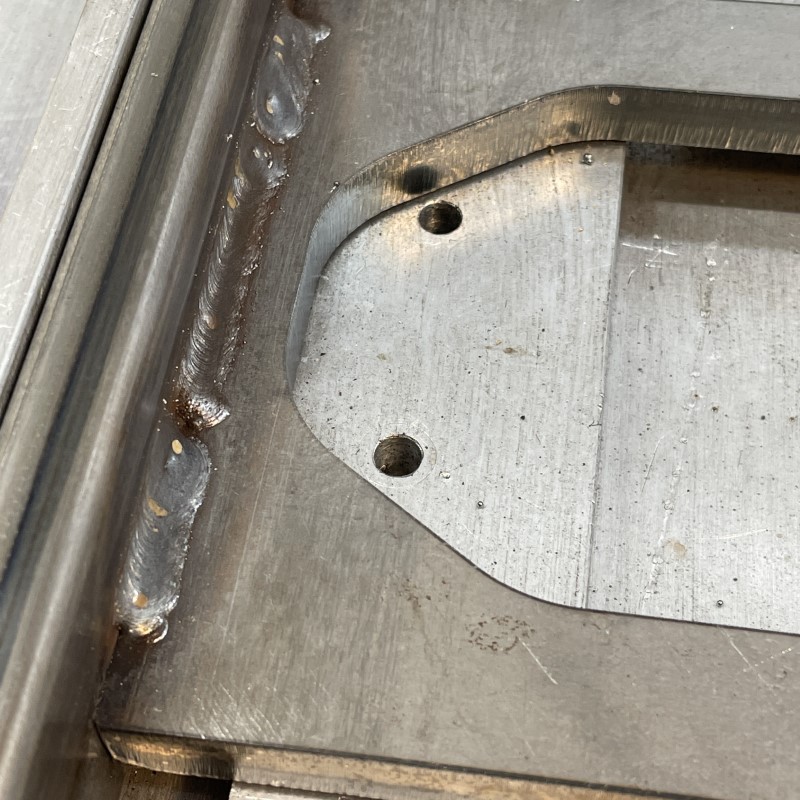
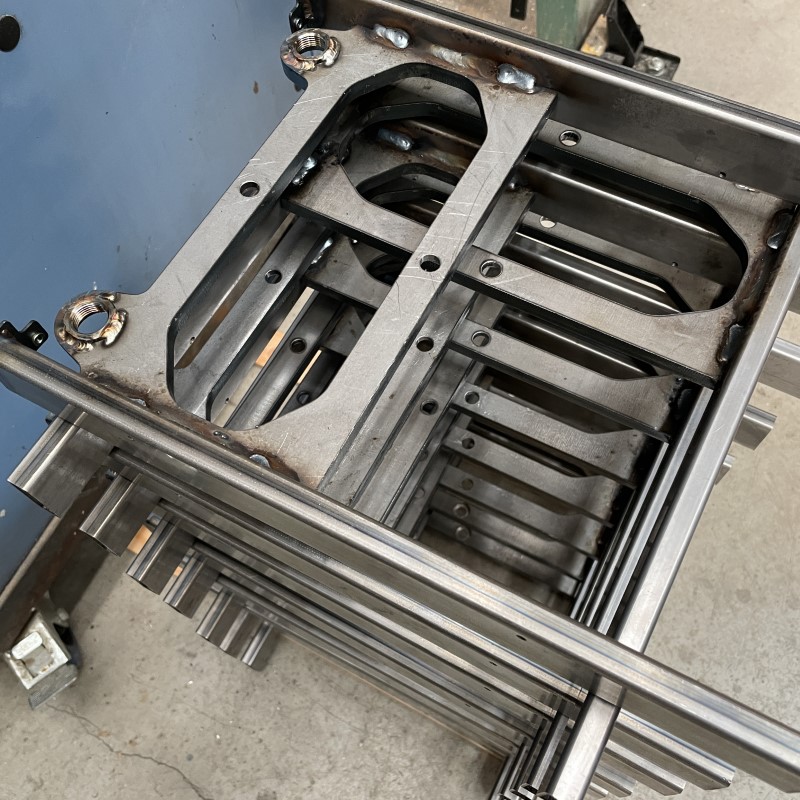
I mentioned that there were a few exceptions to the incremental-type improvements. The first, which is still in development but will should make it into this edition, is a new interface for the electronics. The interface in the first two editions – a very small screen with three control buttons – was located under the cup warmer to protect it from water. A new (slightly larger) screen and capacitive touch interface are being integrated into the splash-proof main electronics housing under the drip tray.
A new PID algorithm, developed and optimized specifically for the DS by an expert in renewable energy systems with a PhD in electrical engineering, brings an entire order of magnitude improvement in boiler temperature stability. What difference does this make to the expresso? None that I can tell as the thermal stability of the massive bronze group casting smoothed out what little variation there was due to the previous algorithm. But ten times better performance is still ten times better – how can you say no? Oh, and I nearly forgot that we now also have a formed drip tray insert that radically diminishes standing water – no more puddles.
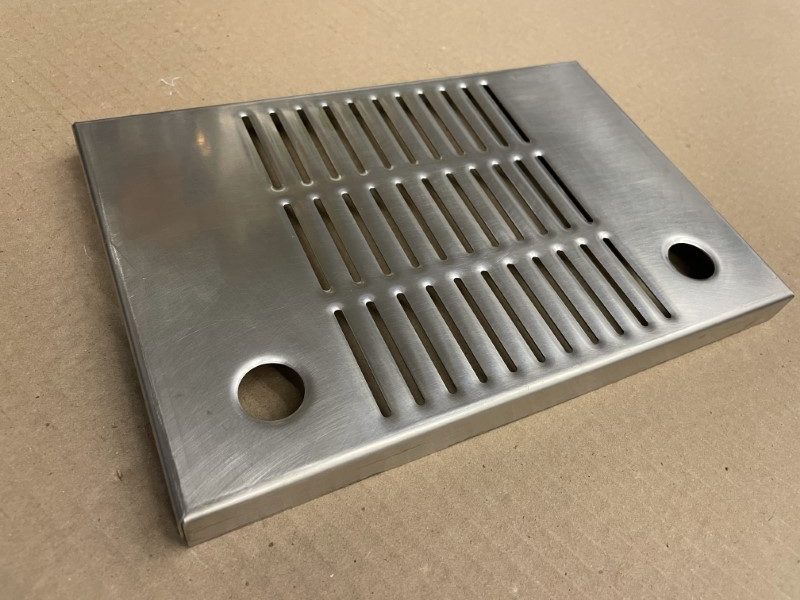
And there are also the coffee tools of course, DS owners get an automatic 15% reduction on all the Lapera tools and we will powder-coat them to match any custom colors.
E61 slip-on shower screen compatibility opens up some interesting options. Lessons to share from testing the different configurations? Sounds like testing aligns with what Londinums use. Curious what effect something like the Matrix would have.
The (my) Matrix screen was one of the screens tested. I don’t remember what Lapera found out, but I would say that the Matrix is perhaps best used with a conventional rotary pump machine due to the Matrix’s backpressure. One of the characteristics of a traditional lever machine is a very fast initial flow/fill rate, and the Matrix dampens this behaviour in the lever machines that I tested. I did not test the Matrix with the Lapera.
I would love to hear more about the improved PID algorithm
Tuning PID systems is regarded by some as a dark art requiring midnight candle-lit sessions and the sacrifice of small mammals.
I implemented a good PID algorithm the first time around, but I didn’t spend an enormous amount of time tuning it. Once I saw that it would get the boiler to temperature without too much overshoot and maintain it there with enough temperature stability at the brew reservoir under variable load (shots, steam and hot water) I moved onto the next task in a very long list of tasks. “Enough stability” in this case being a ten-fold increase by comparison with the already fairly good results from the high-quality pressurestat that it replaced.
The new algorithm is tuned using knowledge of the system: by measuring the energy consumption required to maintain the system at idle over a long time we know what the system losses are. The measured system loss gives us the expected “normal” Duty Cycle for the control system required to maintain the boiler at the idle temperature. The heating element inside the boiler can only be turned on or off – 1400 watts or 0 watts – there are no intermediate states. Instead we turn the element on and off according to the Duty Cycle. A 100% DC means the element is always on, a 10% DC means that it is for 10% of the time. Once we know what the expected DC is, we can just start from that and use the Integral portion of the PID equation to correct for the Error, i.e. the difference between the desired and the measured temperature. Simply put, each time the Error is measured it is added to or subtracted from the Duty Cycle. If the Error is large it will very quickly move the DC to 0 or 100% – if the Error is small, the corrections are correspondingly small. This results in about an order of magnitude improvement over the previous version.
Sounds like the PID tuning architecture could potentially serve as a great advancement for more simplicistic future Lapera offerings (fingers crossed)
Please tell me a date when the 3rd generation will be built.
Thanks
Michael
Hi Michael, the 3rd edition is already in production.