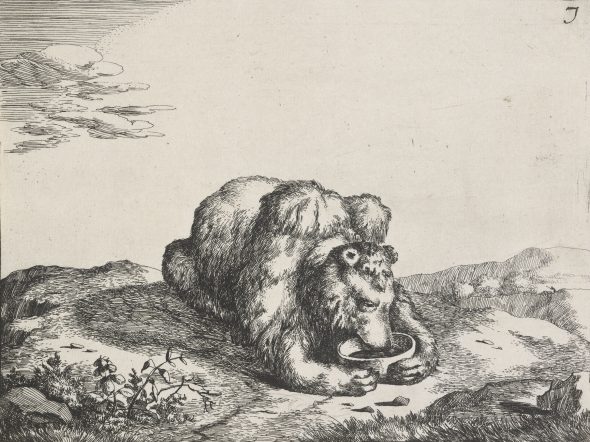
The set of the bears. Plate 7, 1664, by Marcus de Bye, after Marcus Gheeraerts I, 1559. Gift of Bishop Monrad, 1869. Te Papa (1869-0001-67)
Though I’ve run out of three bears analogies, I’ve stuck with the story’s structure: first the porridge was too hot, then it was too cold, and finally Goldilocks found one that was just right. This iteration of the HX caused me to take my hat off, yet again, to the Italians. Many months ago, Dr. Pootoogoo brought a boiler from a later-model Brugnetti to my studio. The flange bolts were so badly rusted that it wasn’t ever going to go back into service without replacing them. It happened to be one with a diagonal HX that I hadn’t examined before and it inspired my to try a similar concept with the horseshoe HX prototype. I was quite surprised that the 60ml HX (baby bear) didn’t deliver water that was cooler than the brew reservoir temperature even though the HX volume was close to the 50ml shot volume. I also started thinking about what the ‘correct’ temperature for the brew reservoir should be. It occurred to me it might not be the best thing for it always to be the same. For example: if the group is at 75 C and the water coming in is at 102 C, the resultant water temperature at the puck is 92 C (these are roughly the numbers for both vintage machines) and we know that the group gains heat after a shot, let’s say for the sake of argument it gains 3 degrees and requires about 2 minutes per degree to recover i.e. 6 minutes. It follows then that for the next shot, if it is to be pulled [i]before the end of the recovery time,[/i] it would be preferable to have the brew reservoir water at a lower temperature than 102 degrees so that when it reaches the puck it will be at same magic 92 degrees. Because of the difference in thermal properties of the materials (i.e. the brass group and the water) and their relative volumes (i.e. big thermal mass of brass vs 50ml of water) it isn’t a one to one relationship. But it is linear – i.e. it will be a constant times the temperature rise of the group. So at any given time during group recovery, the required brew reservoir temperature is the reservoir idle temperature minus the group temperature rise times some constant. In math not English:
Tbr = Tbr_idle – K(Tgroup – Tgroup_idle)
In other words if the heat gain curve of the group could be inversely mirrored by the brew reservoir, then water will be at the right temperature when it reaches the puck [i]no matter when it is pulled[/i]. This is really just destructive wave interference:
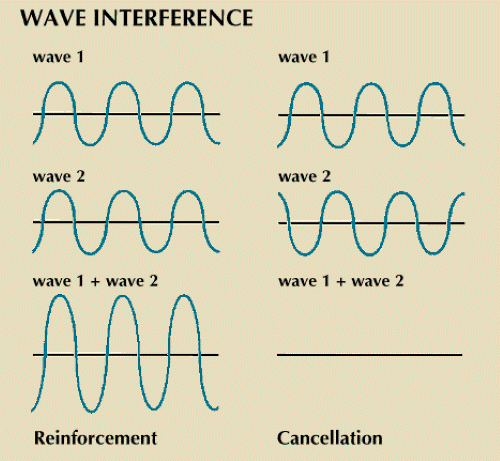
If the brew reservoir temperature curve is positive (i.e. there is heat gain), then it will compound the problem of heat gain at the group. But if the brew reservoir temperature drops after a shot, then it will compensate.
The diagonal HX design consists of a large diameter pipe which connects directly to the back of the brew reservoir – essentially increasing the volume of the brew reservoir four-fold. In fact, the concept of the brew reservoir is pretty much gone altogether in this design – the group flange actually becomes one end of the heat-exchanger. A small diameter injector tube runs through the middle of the large diagonal pipe. Line water comes in through the injector too fast for the surrounding water to heat it to boiler temperature and mixes with the water behind the group to get the really stable results that we saw in the earlier testing.
I replicated the basic principal minus the diagonal tube and in so doing figured out why the diagonal design ended up that way i.e. diagonal.
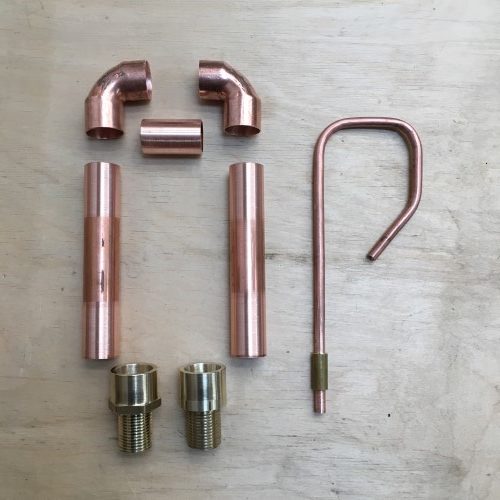
The last kink in the 6mm tubing was only way to thread all the larger diameter fittings onto the injector. And this is a one-way operation: once it is brazed together you can’t take it apart again.
Brazed and (sort-of) cleaned.
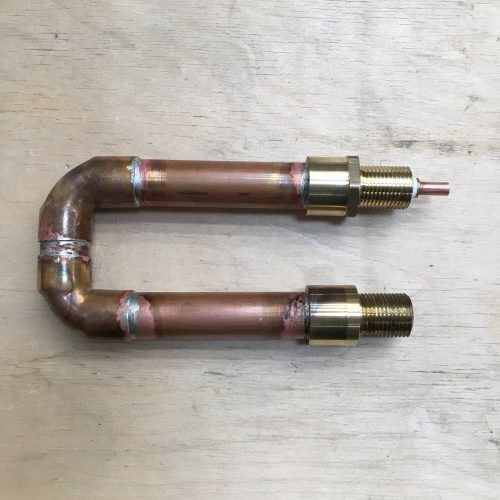
And here are the results:
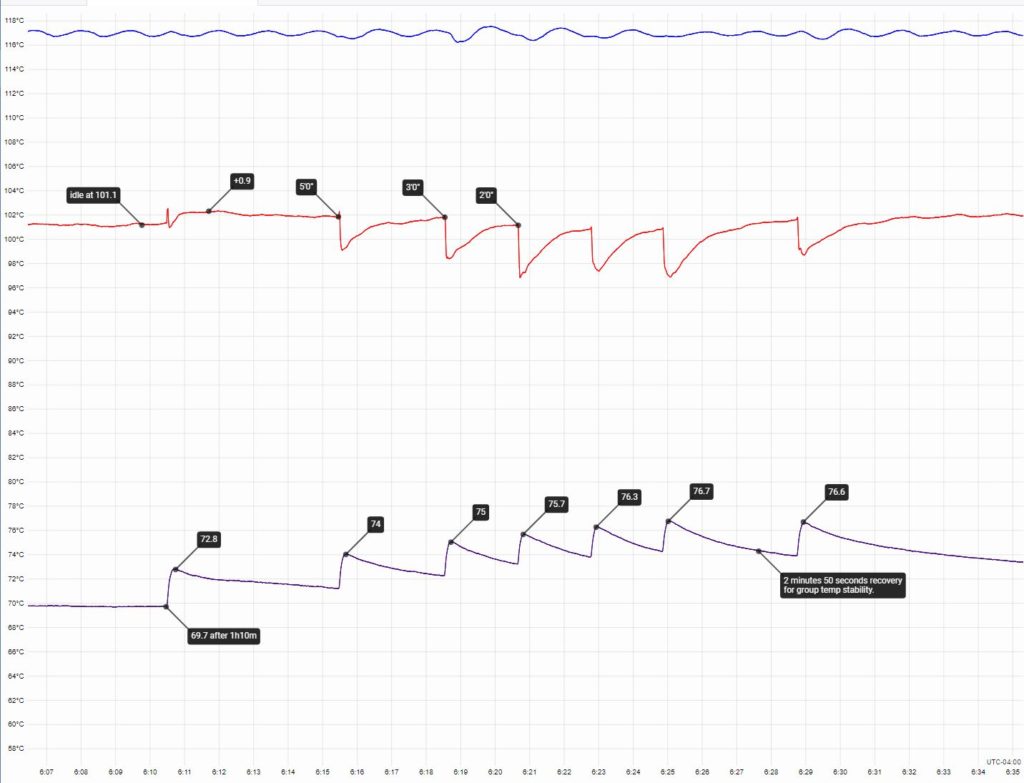
Blue – Boiler
Red – Brew reservoir
Purple – Group neck
Now, although the results aren’t perfect, it shows that the concept works. The group heat gain for successive (unnaturally) rapid shots has been significantly diminished and the recovery time for the group is less than half of what it was (less than 3 minutes). The length of the injector plays an important role in how much boiler temperature HX water mixes with the line water and consequently in the temperature of the water that reaches the brew reservoir. But, as I said, this is a one-shot fabrication and is too much trouble to alter. It would be much easier to change and/or maintain if the injector tube screwed into a straight length of larger diameter tube that maybe ran directly to the group right through the boiler, maybe on a diagonal…
Wait – someone already thought of that.
Enough porridge already.