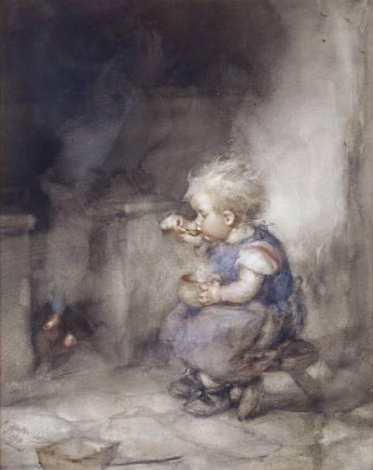
Hot Porridge, Hannah Clarke Preston MacGoun, 1910
[Ed: re-post from Nov 17, 2018]
The new results in my ongoing quest for Goldilocks porridge (aka boiler-group thermodynamic interaction and stability, but porridge sounds much better) are in and I have to say that I’m rather pleased.
What are we testing?
This is temperature profile of the new boiler with diagonal HX and injector. The boiler and the HX chamber are both made of stainless steel but, unlike the previous Horseshoe HX prototype, the brew reservoir is now bronze (for reference, stainless is roughly 20 times less thermally conductive than copper and copper-based alloys). The diagonal HX configuration eliminates the separation between the HX chamber and the brew reservoir and they both form one single volume of hot water at a lower average temperate than the boiler water. Cold water is injected directly into this volume and the resulting mix, now at a lower temperature, moves on into the group during a shot.
Methodology
Methodology is similar to previous tests: the machine was turned on several hours in advance to make sure that everything is at its ultimate idle temperature. The probes are K-type thermocouples placed in the same spots as prior tests – the only difference being that the brew reservoir now has a dedicated threaded thermocouple socket – no more tape coming unstuck or clamps falling off. Shots are simulated by using a flow restricting valve placed on the outlet of the portafilter.
Shot simulation procedure is:
- Pull
- Pre-infusion 7 seconds (lever in down position) –
- Shot 20-25 seconds for lever to return to the cam inflection point (lever just past straight up and down)
- Post-flow 10-30 seconds (lever returns to rest position)
Various timings between the shots are tried: 5 minutes, 4 minutes, 3 minutes, 2 minutes, 3 minutes.
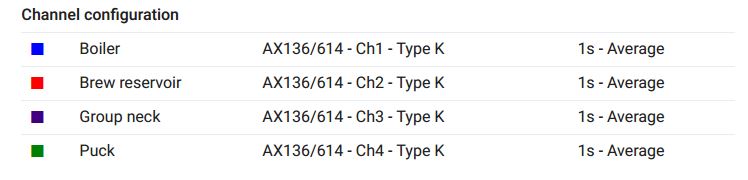
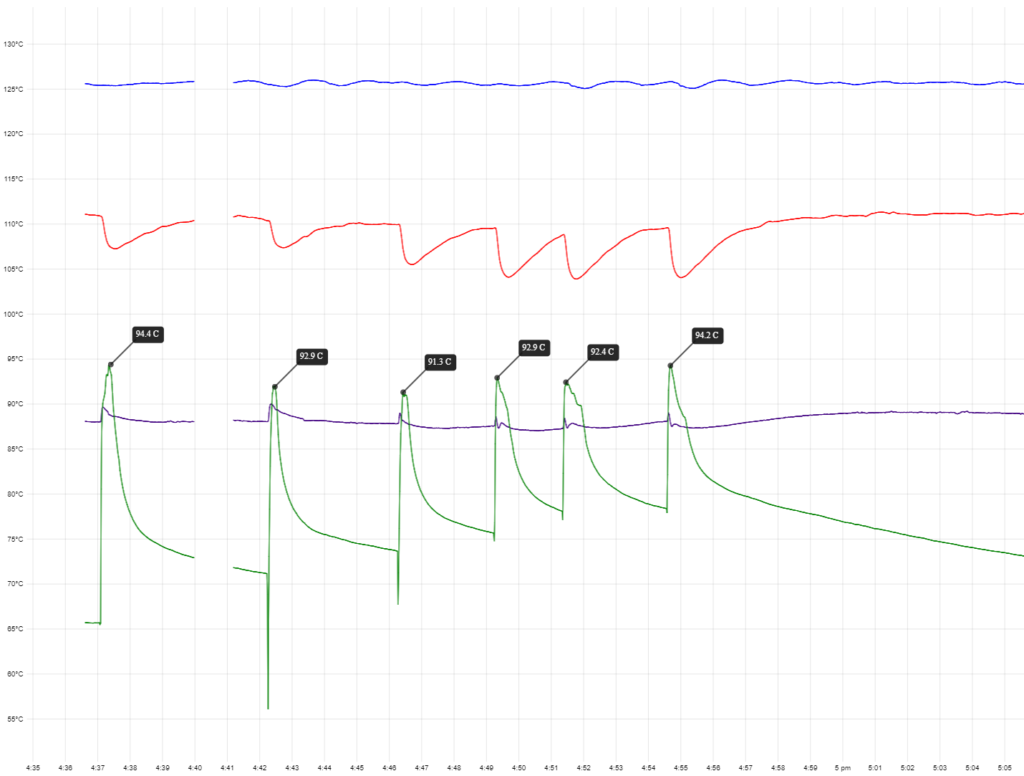
Comments
The pseudoScaceâ„¢ device (puck temperature readings) has too large a thermal mass to give meaningful results for peak puck temperatures when inserted cold. I therefore left it in place, before, during and after the test to minimize its impact. The one second sampling time period is too long to give reliable readings at the moment of the pull. On a few of the shots there is a significant drop seen at the puck at the moment of the pull. I believe that this is due to the piston creating a vacuum as it is raised and drawing cold water back up through the pseudoScace from the waste line. A change in equipment would be required to eliminate this if this hypothesis is correct.
Conclusions and observations
The original Aurora diagonal HX I profiled back in May demonstrated uncanny thermal stability at the brew reservoir, but the group suffered per-shot heat-gain and was slow to return to its baseline idle temperature. These results show that the brew reservoir temperature is dipping significantly but the group and the puck temperatures are, by comparison to the antique machine, rock steady. The maximum overall delta at the puck is 3.1 C (between the walk-up and the third shots) but the inter-shot maximum delta is 1.8 C (the minimum inter-shot delta is 0.5 C for 2 minutes between shots).
Summary
So, to summarize: best performance at 2 minute intervals, significantly lower puck temperature fluctuation than the antique machine and little to no group heat-gain. This, I think, may be a slightly better mouse trap – though not really by design, rather by accident of the thermal interaction of the materials. I’m not going to complain.
If you will permit me, and at the risk of tooting my own horn:
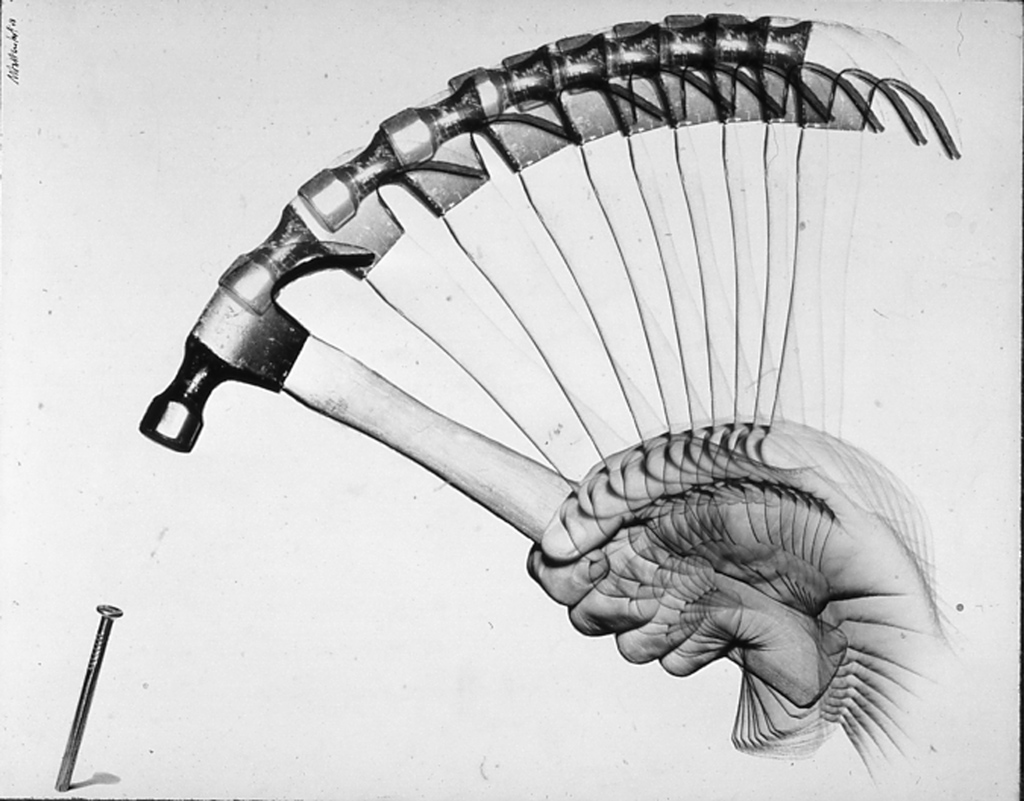
Courtesy of UC Davis, Special Collections
Title: Magazine ad for Bank of America: hammer and nail montage.
Creator/Contributor: Halberstadt, Milton, Photographer