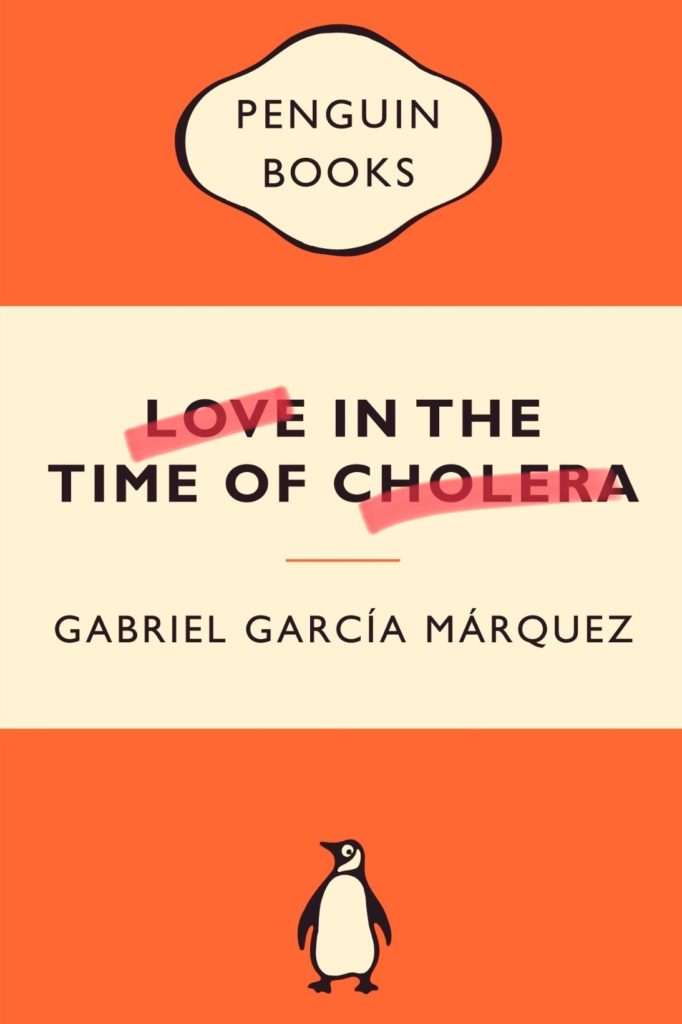
In these strangest of times, I hope that you are all well.
I’m not sure where to begin really. Writing about small goings on in my tiny corner of the vast tableau of human experience seems rather pointless given what the whole of humanity is currently enduring. But in the hope that some may find these musings mildly amusing and possibly a welcome diversion from the cataclysmic car crash of out there, we humbly soldier on.
I took delivery last autumn of the bulk of the sheet metal work from a new Canadian supplier. Since then, the stainless steel covers have been sitting on the shelf waiting for the completion of the frames so that all the parts that need to be painted can go to the shop at the same time. As those of you who follow the posts on that photo site owned by the social media company with the reputation for (among other things) being extremely cavalier about their users’ privacy will know, the frames were finished some time ago. So now it’s time to put the finishing touches on the covers. A long, long time ago, (you know, in 2020BC) I discovered that the straight folds on two front flanges of the cover didn’t have quite enough relief on the interior flanges (gasp) to allow the requisite over-bend during fabrication. The upshot of this is that the front panels are only nearly, not exactly, at 90 degrees to the sides (re-gasp). Always seeking to shave off another minute source of imperfection, adding a tab that connects the front flanges to the sides will resolve this and have the additional benefit of increasing the overall stiffness.
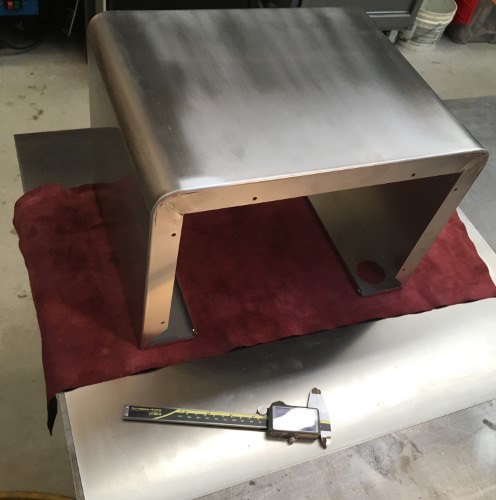
This of course requires a new tool. One strangely reminiscent of an earwig.
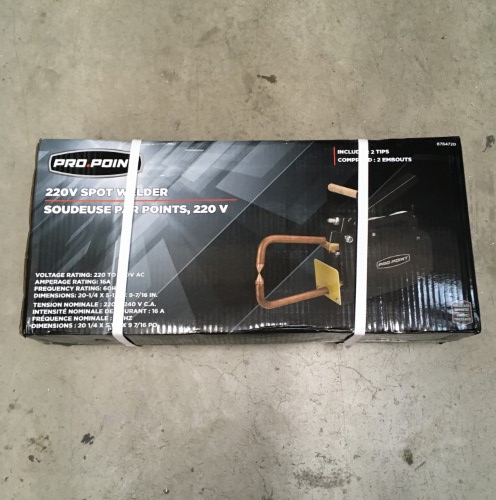
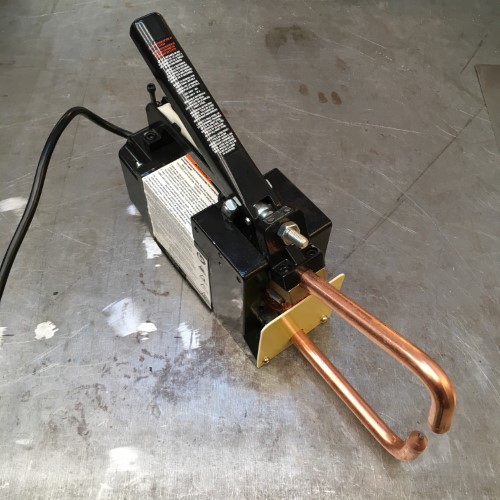
As always, you get what you pay for and this thing is neither terribly expensive nor terribly good. But it will do (some of) the job. As the following test shows, it can produce a mechanically sound, if slightly less than perfect, spot weld.

Bunch o’ tabs cut from some scrap stainless.
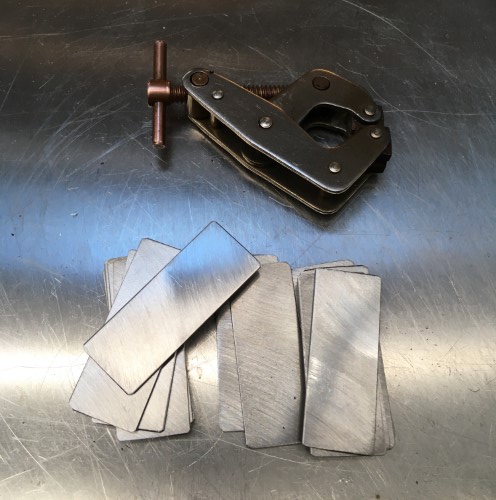
A tab spot-welded into place.
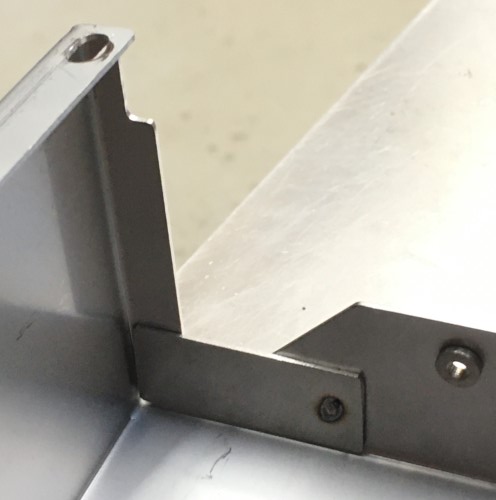
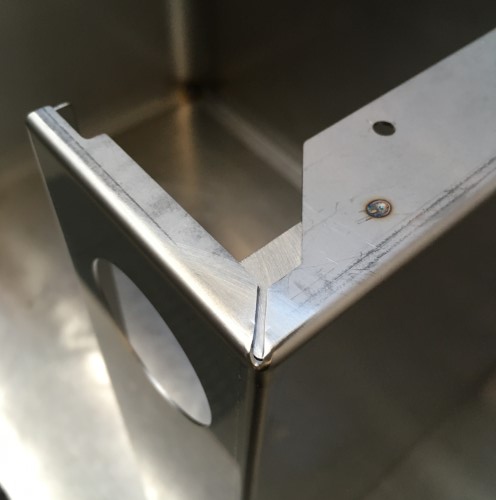
BUT… without radical modification, the spot welder can’t be positioned to make the second weld on the front flange. So, it’s back to the old fashioned (i.e. long and slow) way – TIG welding by hand – with a simple jig to get things all orthogonal-like.
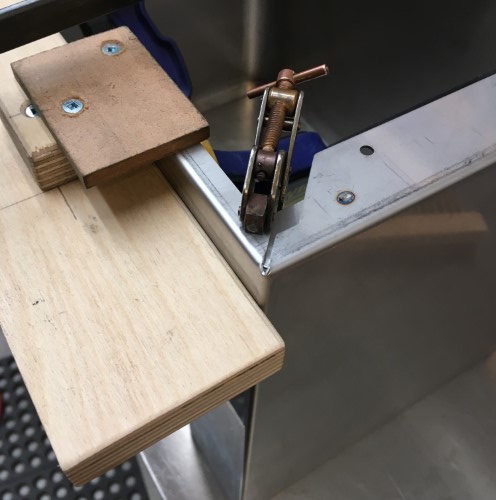
Welding thin material is really easy to get wrong. We managed to pull these off without blowing any holes (or at least ones that I will show you pictures of).
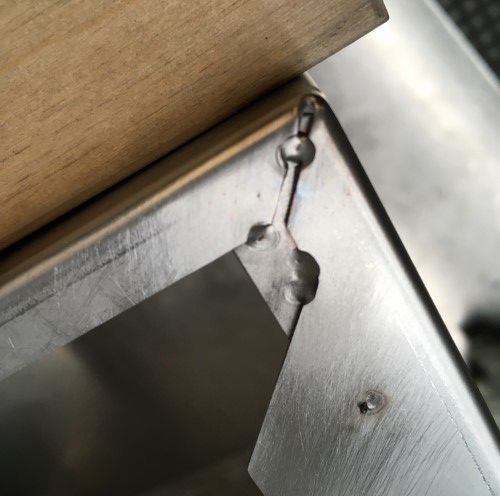
Rinse, repeat:
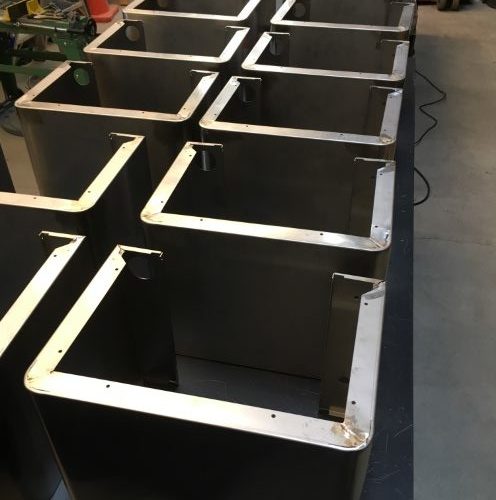
Drive to nearest big-box store for, well, boxes so that they can be shipped to the painters :D
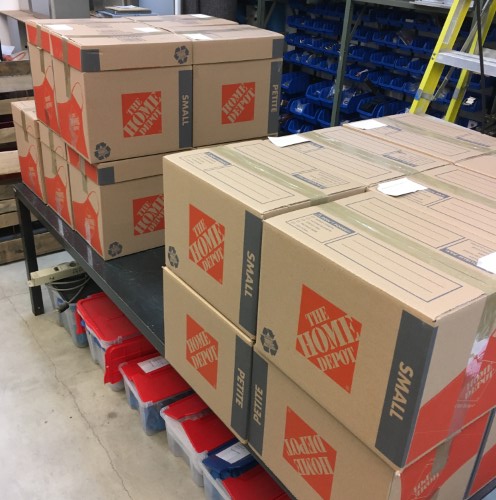
… hmmm, wonder how they turn out.