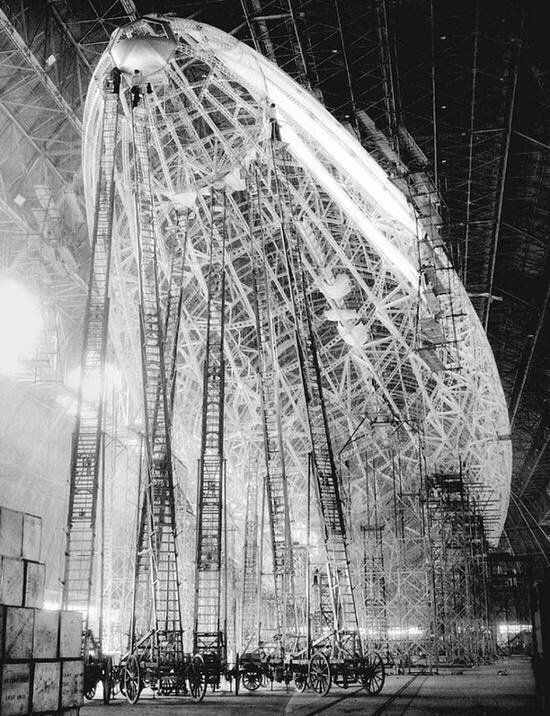
Ok, so I don’t have to climb a ladder quite that big to put the finishing touches on this frame. That is a lot of parts to design, fabricate and keep track of. Without computers. At once humbling and further proof, should any be required, that Zeppelins are insane.
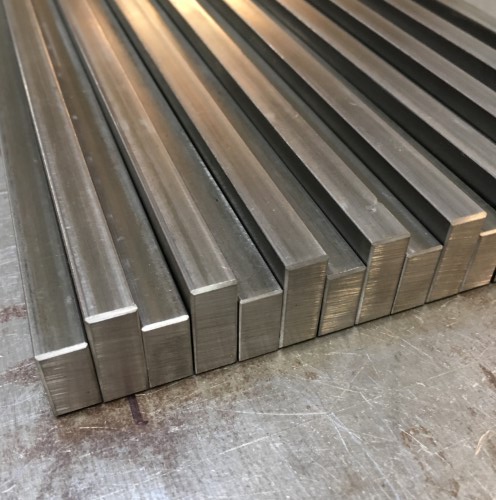
Cross bars made from cold-rolled 1080 carbon steel. The small ones are for the top bar and the large ones for the bottom. These are rough-cut to length and squared and ground (sanded really) to just under their nominal finished length. These parts do not play a role in locating the sides of the frame (the laser-cut parts do that job), but they do locate the group and the taps so there can’t be too much play. In practice this translates to a length of within 0.2mm of, but always less than, nominal.
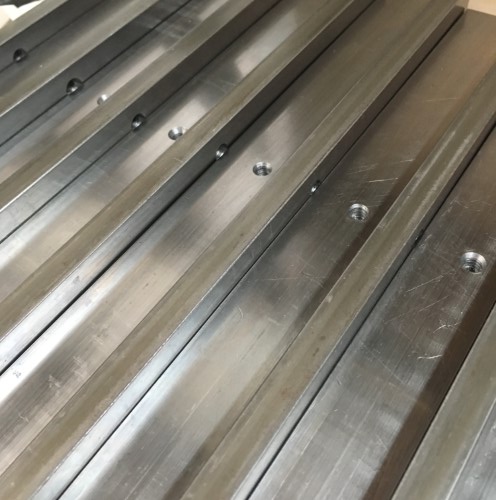
Drilled, countersunk, tapped and deburred.
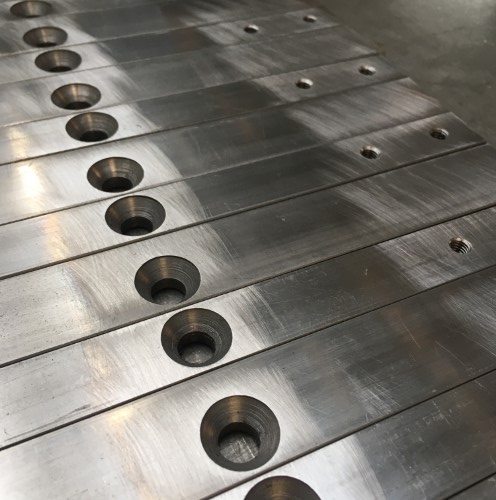
The uprights are cut from lengths of rectangular tubing and are temporarily tagged and machined in pairs. This means that the left and right halves of each pair is the same length and, where necessary, hole placement is symmetrical. The baby 1″ clamps are made by Kant. The design with the central pivot eliminates twisting so the clamping force always remains axial between the jaws. Consequently, parts don’t slip out of alignment as the clamp distorts when they are tightened. Very clever, very useful.
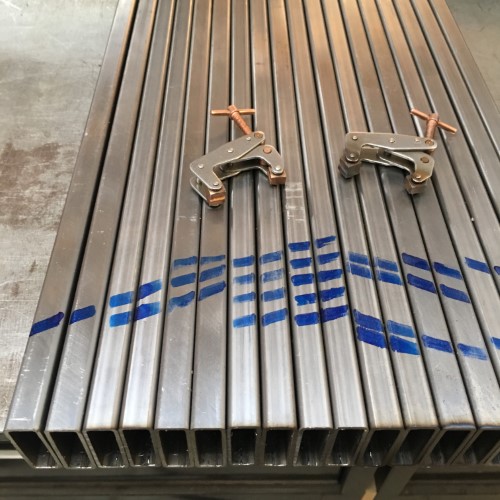
The tops of the tubes will be filled with a coupon of 1/8th steel which is drilled and tapped for the ball studs that hold the cup warmer in place. This is the first time that all of the parts of this iteration of the design are being assembled so the coupons are left blank in order allow adjustment of the hole position, if necessary. Once I know that everything fits as it is supposed to the holes can be laser-cut the next time this part is ordered.
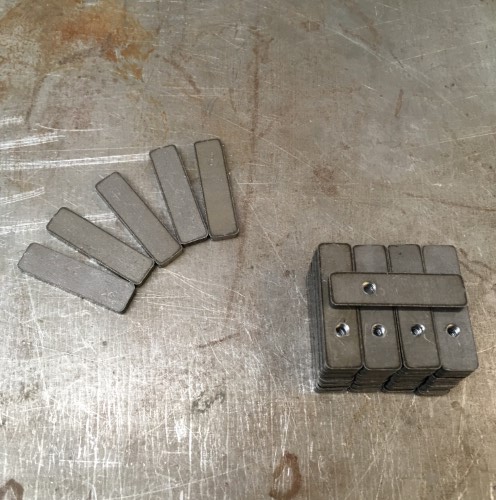
All of these things meet each other for the first time in the upright frame assembly. <digression> Interesting word thing. At some point in my education I learnt that the English word “thing“, along with its German and Dutch cousin “Ding/ding” and Scandinavian “ting“, original meant assembly, as in an assembly of people. A thing was a gathering of the populace to legislate, adjudicate and elect leaders. In other words, it is a precursor to our courts and parliaments rolled into a single time and place. For the Vikings, “Are you going to that thing on Friday night?” meant finding out how many pounds of salt cod your neighbor Leif owed you because his son Svend borrowed your longship without asking and crashed it. </digression>
The pieces are brought together in the jig along with an extra spacer-bar across the top that will not be welded in place. In this particular jig, the left side and bottom rails are installed permanently perpendicular to each other while the rest of the transverse parts are allowed to move slightly from right to left. This permits clamping and means that the frame can be removed from the jig despite the inevitable slight distortion to the thin walled tubing that occurs during the welding.
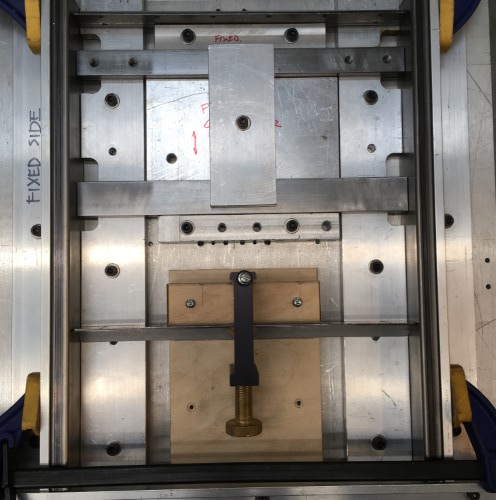
After beefing up all of the fragile tack welds, the sections of the frame can now finally be united with the words: with this TIG I thee weld. Though admittedly an actual three-way wedding would be a little weird. Front and upright.
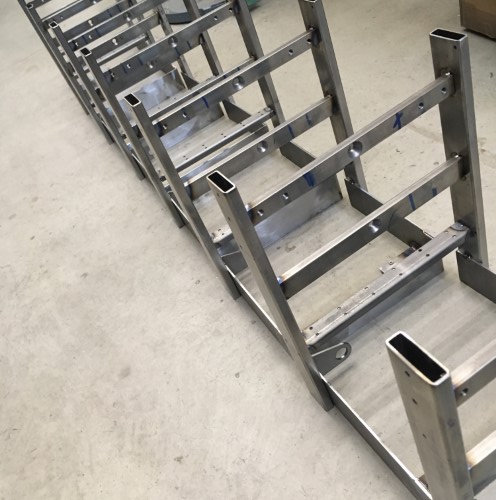
Back, front and upright held in place against carefully aligned stops welded to the table.
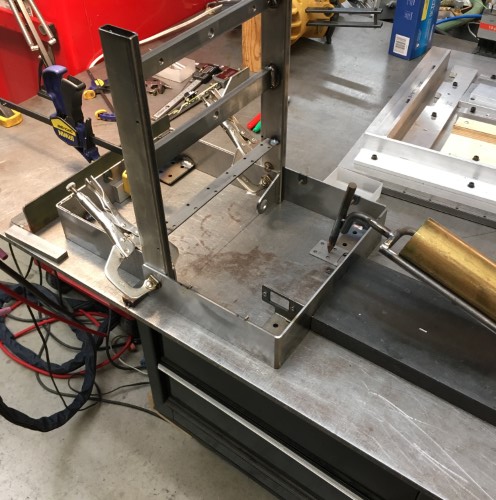
Almost complete!
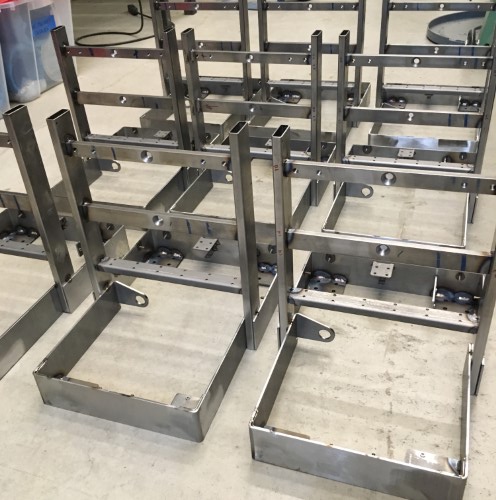
Now that the tubes are in their final place the end fillers can be located and fixed with a delicate weld. The gaps are left purposefully so that welds don’t have to be ground where they would interfere with other parts.
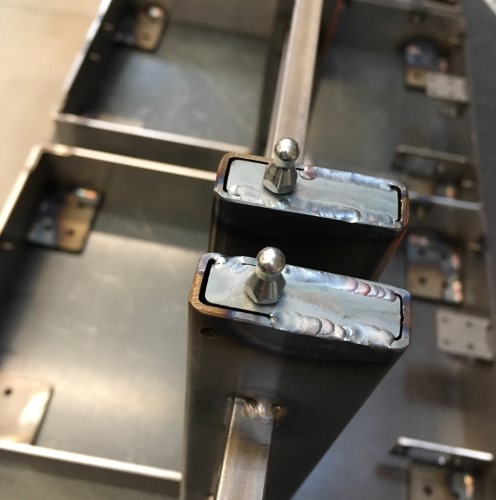
A satisfying row of finished frames cooling with a vintage bicycle…
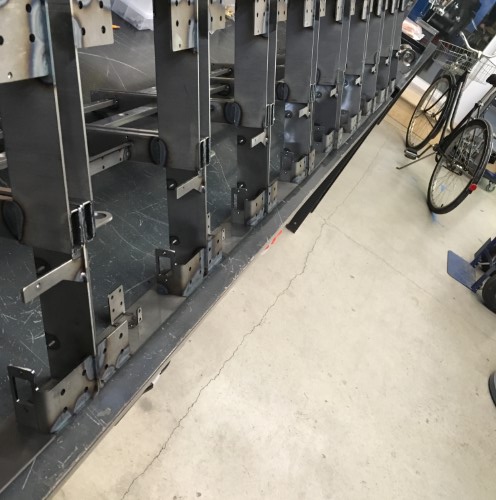
The next step is to cover them in a skin made of cotton painted with aluminum, put a gas bag made from cow intestines inside, fill them with hydrogen and fly them to New York. Perhaps not. (What were they thinking?)